By Vishal Patel, M.S.C.E., P.E., Todd DeMico, P.E., and Sebastian Lobo-Guerrero, Ph.D., P.E.
INTRODUCTION
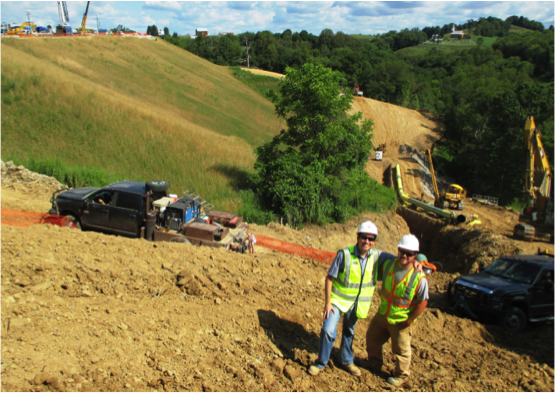
Common techniques for stabilizing large scale slopes (i.e. rock toes, buttresses, soil nails, retaining walls, etc.) are sometimes impractical from both a constructability and stability point of view. Slope stabilization with deep foundations, while effective, are not widely used due to a lack of published standardized design procedures. American Geotechnical and Environmental Services (A.G.E.S.), Inc. had the opportunity to design an embankment stabilization system using drilled shafts. Drilled shafts were chosen for the site based on unique construction conditions and the overall scale of the proposed embankment. A.G.E.S., Inc. was also involved during construction of the project and had the opportunity to observe the general performance of the system.
CASE STUDY
This case study involves the installation of a pipeline at the toe of an existing 110-foot-tall embankment (see right) constructed within a known ancient landslide. Construction for the project required excavation for the pipeline in addition to a 50 foot wide bench near the existing toe for construction access. In order to accommodate the bench width, an additional 45-foot-tall embankment below the existing 110-foot-tall embankment needed to be constructed. The size of the embankment and the inherent weakness of the soil within the ancient landslide required consideration of techniques beyond the traditional slope stabilization methods to meet an acceptable factor of safety and a very limited time frame for construction. A total of 75, 3-foot-dimeter, drilled shafts reinforced with W beams, embedded into bedrock, were designed and constructed in 3 rows along the embankment to provide adequate stabilization.
Analyses for excavations along the proposed final slope were performed along the existing embankment. The analyses were performed to ensure the pipeline excavation, the 50-foot-wide by 300-foot-long bench, and the proposed treatments below the pipeline, would not result in instability of the existing embankment. The space for the bench resulted in the final slope extending approximately 45 feet lower in elevation to reach flatter grade. As a result of the bench, the pipeline was to be installed in a backfilled excavation consisting of both the upper 110 foot tall existing embankment and the 45-foot-high stabilized embankment. The slope at the lower portion was to maintain the 1.3H:1V orientation of the existing ground surface.
GEOTECHNICAL ANALYSES
Drilled shafts were proposed to minimize disturbances to the existing soils. Design for the proposed slope retrofit consisted of performing geotechnical and structural analyses for both global stability of the proposed treatment and lateral analysis of the proposed drilled shafts. The two analyses were performed sequentially to ensure that the proposed layout satisfied these geotechnical and structural requirements.
Stability analyses were performed using SLIDE for both the upper slope (the existing embankment above the pipeline) and the lower slope (the proposed slope treatment region below the pipeline). The slope treatments were designed to satisfy a factor of safety of 1.3 for the temporary condition and 1.5 for the permanent condition. These analyses were performed to ensure that the proposed embankment work would be stable for both construction and permanent conditions. In an effort to minimize soil disturbances at the toe of the slope, rigid elements (drilled shafts) were chosen as the preferred option. The drilled shafts were modeled in SLIDE as a resisting force. Based on the required resistance, the pile layout was determined from the SLIDE analyses. Lateral analyses (p-y model) were performed using LPILE in order to size the rigid elements and ensure drilled shafts extended deep enough in order to satisfy a fixed condition.
The drilled shafts consisted of W-piles encased within concrete (see left). Bending and shear resistance were analyzed considering the 50 ksi steel piles only. The analysis considered a spacing of the drilled shafts along each row equal to three times the drilled shaft diameter (3xD) in order to maximize passive resistance due to soil arching. The spacing in between rows was chosen to avoid “shadowing” and group effects that could potentially reduce the shaft resistance.
CONCLUSION
The design procedures for stabilizing slopes with deep foundations such as drilled shafts are still in their infancy. Although several publications exist for this stabilization technique, none are widely accepted nor considered design standards. This manuscript described a simplified design procedure based on global stability and lateral deformation analyses as suggested in the literature (for example FHWA and ODOT design manuals). A.G.E.S., Inc. was able to witness the constructability of this design alternative and did not find any indications of instability. This suggests that the implemented design procedure provides and adequate factor of safety. As projects like these begin to gain momentum, particularly in the public sector, the procedures for design will become more common.
A manuscript describing in detail the implemented design procedure is being developed by the authors and it is expected to be presented at ASCE-GI/DFI/ADSC/PDCA International Foundations Congress and Equipment Expo (IFCEE) 2018 in Orlando Florida.