Pittsburgh’s long industrial past includes a history not only in steel, but also in aluminum, glass, and transportation. Since the 1980’s, much of this industry-based economy has since transformed to tech-based commerce such as robotics, medicine, and education. And as the industry-based companies closed shop, they left behind land that had been exposed to various industrial compounds. This brought about a tricky problem: what should Pittsburgh do with these former industrial sites, or brownfields.
Brownfield is classified as a “real property, the expansion, redevelopment, or reuse of which may be complicated by the presence or potential presence of a hazardous substance, pollutant, or contaminant.”(HR-2869-2002) Pittsburgh was a city of industry, and therefore is also city of many brownfields. The economic transformation of Pittsburgh required innovation in brownfield redevelopment.
On September 11th, 2014, EWRI hosted a 2-part seminar on brownfield redevelopment and remediation. During the first part of the seminar, Dr. Deborah Lange, executive director of Western Pennsylvania Brownfields Center, described the complex, multi-disciplinary requirements of brownfield redevelopment. Neighborhoods such as Braddock, Hazelwood, South Side Works, and East Liberty were used to describe the nine key characteristics that must be considered when redeveloping a brownfield.
- Community engagement
- Historical relevance
- Infrastructure
- Remediation needs
- Optimal use of the land
- Multi-jurisdictional cooperation
- Political commitment
- Public-private partnerships
- Socio-economics
Despite the complications that each brownfield brings, Pittsburgh has endeavored to transform these former industrial sites, resulting in many success stories.
The second part of the seminar focused on novel remediation strategies of a series of compounds that have long contaminated many brownfield sites, chlorinated solvents. Chlorinated solvents were utilized by many industries as cleansers, degreasers, thinners, or resins. Long-term exposure to chlorinated solvents results in damage to the nervous system, liver, or kidneys, and in some cases lead to cancer. Unfortunately, industry’s historic use of chlorinated solvents has lead to current widespread contamination in the groundwater.
Fortunately, many innovative technologies are now being used to reduce the chlorinated solvent contamination. The second part of the seminar featured Dr. Udai Singh, Vice President of CH2M HILL, with a long-term experience in modern remediation techniques. Dr. Singh described the latest practice of groundwater remediation that has been proven reduce chlorinated solvents concentrations. These technologies include:
- In situ thermal treatment: the contaminated subsurface is heated, mobilizing the chlorinated solvents, which are then extracted and treated
- Soil mixing: contaminated soils are mixed with reagents such as zero-valent iron, oxidants, or bentonite to react/stabilize the chlorinated solvents
- Air sparging/ soil vapor extraction: air is injected in the contaminated subsurface, and volatile chlorinated solvents are extracted and treated
- In situ bioremediation: organic substrates such as lactate, whey, or vegetable oils are injected in the contaminated subsurface, promoting biodegradation of the chlorinated solvents
- In situ chemical oxidation: strong oxidizing agents are injected in the contaminated subsurface, reacting and degrading the chlorinated solvents.
Preliminary studies have found these technologies capable of reducing the chlorinated solvent concentration by 95-99%. Dr. Singh noted that the technologies varied in cost, with soil mixing as a low-cost remediation solution, and in situ chemical oxidation as a higher cost alternative. However, each innovative process had various advantages and disadvantages, demonstrating there was no silver bullet to chlorinated solvent remediation.
Interested in other EWRI-PGH seminars? Visit http://www.asce-pgh.org/EWRI for upcoming events.
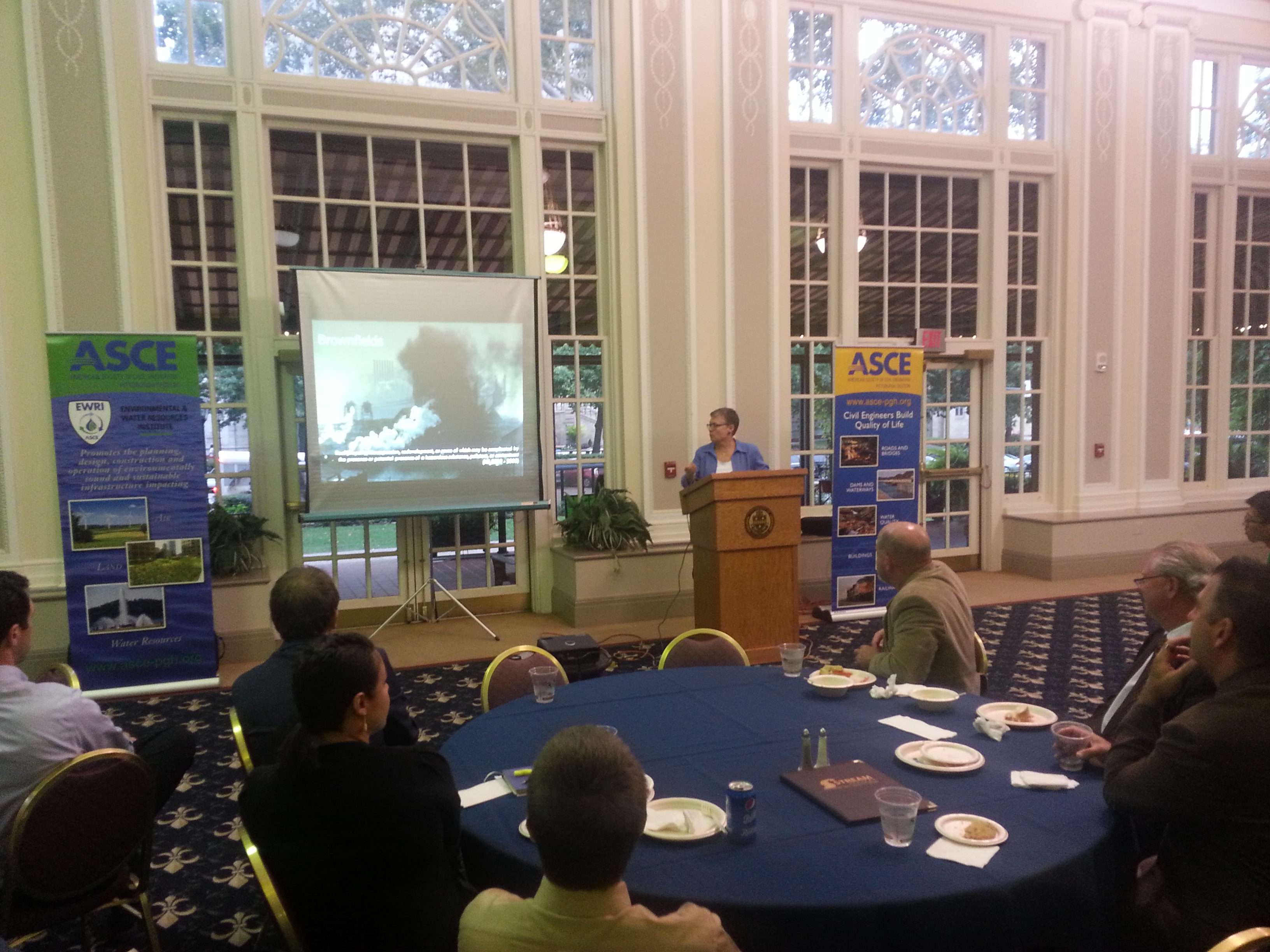